Note: Forming a Large Steel Tube
Objective:
Heating an area around elliptical hole in steel tube prior to forming; the client had been using a torch for this application.
End Product:
Steel tube
Equipment:
Ambrell EKOHEAT 150 kW, 5-15 kHz solid state induction heating power supply with a workhead and coil specifically designed for this application.
Materials:
Steel tube
Temperature:
1800 ° F (982 °C)
Frequency:
7 kHz
Testing:
A custom-designed single position multiple-turn pancake coil was built to generate the required heating for this application. Initial tests were conducted to optimize the power delivered to the part. The coil was separated from the part by two layers of insulating felt. The coil needed to be weighted down with cinder blocks to prevent levitation. An optical pyrometer was used to measure the temperature of the inside of the part. It took about 40 minutes to reach the targeted temperature of 1800 °F (982 °C).
Benefits:
-
Speed: Induction met the client’s time requirements and is generally faster than other heating methods.
-
Precise Heating: Induction can be applied almost exactly where it is needed without wasting heat where it isn’t required.
-
Repeatability: The client can expect the same result in the same amount of time every single time with induction heating.
-
Torch heating is often dependent upon operator skill.
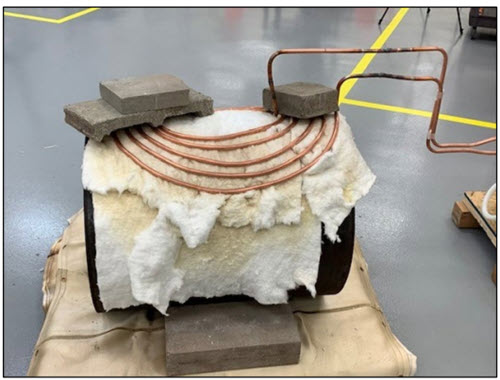
Visit our Applications Lab to learn more about free applications testing.
1655 Lyell Ave, Rochester, NY 14606 USA | Tel: +1 585 889 9000