Note: Heating rods for thread rolling to create fasteners
Objective:
To heat carbon steel rods to temperature for hot forming/thread rolling to create fasteners
End Product:
fasteners
Equipment:
- Ambrell EKOHEAT 250 kW, 5-15 kHz induction heating power supply with a remote workhead
- A channel induction heating coil designed and developed for this application
Materials:
Carbon steel rods (20 mm/0.79” OD & 100 mm/3.94” height)
Temperature:
1382 °F (750 °C)
Frequency:
7.5 kHz
Testing:
The client was cold forming, but wanted to switch to hot forming to increase throughput and enhance product quality. Cold forming requires cutting, while hot forming pushes the rod into shape against a die. This is part of an automated line. The system was sized and the coil was designed to ensure 45 parts per minute can be heated to the temperature required for hot forming.
Benefits:
-
Speed: Switching from cold forming to hot forming offers increased throughput
-
Repeatability: Induction is highly repeatable and easy-to-integrate into manufacturing processes
-
Quality: Induction often results in stronger, more durable threads
-
Economy: Hot forming results in less tool wear and increased tool life when compared to cold forming
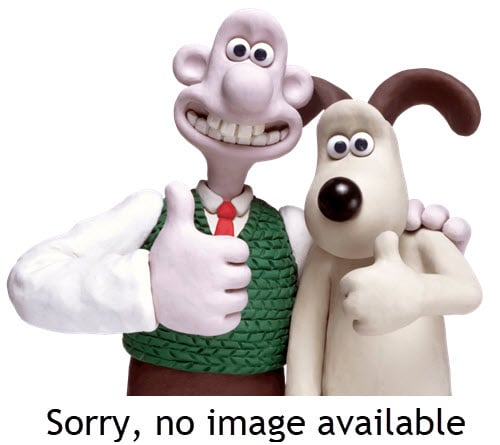
Visit our Applications Lab to learn more about free applications testing.
1655 Lyell Ave, Rochester, NY 14606 USA | Tel: +1 585 889 9000