Note: Copper block & carbide; contact assembly
Objective:
To heat a copper block with carbide to temperature for a brazing application; the client was using a gas oven previously
End Product:
Electrical contact shoe
Equipment:
Ambrell EKOHEAT 15 kW, 50 to 150 kHz induction heating system equipped with a remote workhead containing three 1.5 uf capacitors for a total of 4.5 uf A single position three-turn helical induction heating coil designed and developed specifically for this application
Materials:
- Copper block (2.25” x 2.6” x 1.12” / 56 mm x 66 mm x 28 mm)
- Carbide
- Black flux
- Braze alloy
Temperature:
1600 ºF (871 ºC)
Frequency:
80 kHz
Testing:
The parts were fluxed and a shim was created to match the side profile of the carbide. The braze shim was placed on the fluxed part. The braze shim was then fluxed and the carbide was placed on top and fluxed as well. The assembly was then placed inside the coil and power was turned on. The coil was set to a height to primarily target the copper block because it was the largest heat sink on the thermal system. After four minutes the assembly was at temperature, the braze alloy had flown throughout the joint area and heating was completed. The assembly was then placed in an acid bath and scrubbed to clean it up.
Benefits:
-
Speed: Induction enabled the brazing process to be completed more rapidly than with an oven
-
Precise heating: Induction can supply heat exactly where it’s needed
-
Efficiency: Induction delivers heat only where it’s required, and it’s an instant on/instant off method
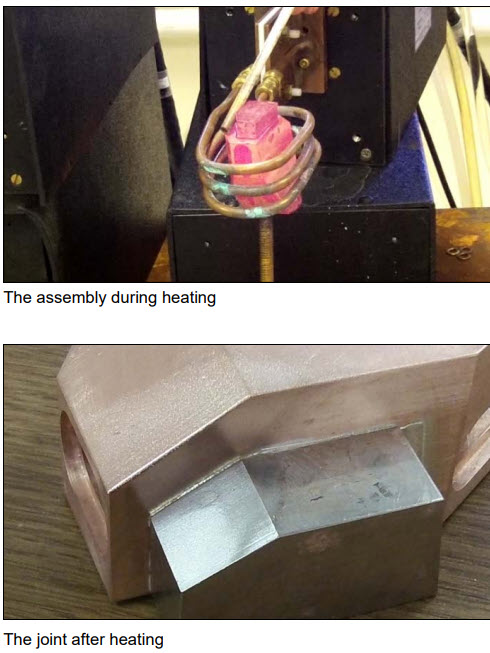
Visit our Applications Lab to learn more about free applications testing.
1655 Lyell Ave, Rochester, NY 14606 USA | Tel: +1 585 889 9000