Note: Brazing copper tubing and brass fittings (aerospace)
Objective:
To braze .125 in (3.18 mm) copper tubing and .25 in (6.35 mm) brass fittings to create aerospace parts. This would replace a brazing torch that takes 2-4 minutes.
End Product:
Aerospace parts
Equipment:
Ambrell EASYHEAT LI 0224, 2 kW, 150-400 kHz induction heating system equipped with a remote heat station containing two 0.33 μF capacitors A single position, three-turn helical induction heating coil designed and developed specifically for this application
Materials:
Flux Braze alloy .125 in (3.18 mm) copper tubing .25 in (6.35 mm) brass fittings
Temperature:
1200 °F (649 °C)
Frequency:
331 kHz
Testing:
Braze material was placed on the part, the part was fluxed, and it was placed inside the coil. The EASYHEAT LI 0224 was turned on, and braze alloy flowed across the joint. The part was heated to the desired temperature within 45 seconds.
Benefits:
-
Improved quality and repeatability: Induction heating achieves superior process repeatability when compared to a brazing torch and a more predictable end product which enhances quality
-
Higher production rate: With the target temperature being reached at less than half the time it took with the brazing torch, significant time is saved which will improve the production rate
-
Superior efficiency: Induction heating applies heat only to the part, which means there"s no wasted energy and cost savings are achieved when compared to a brazing torch
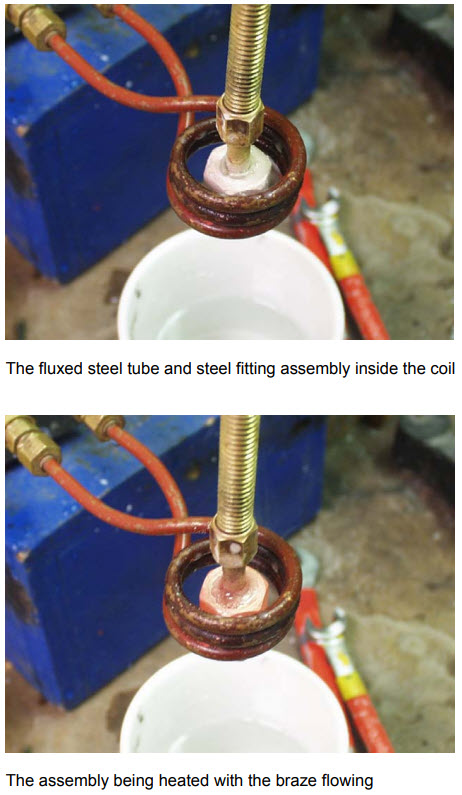
Visit our Applications Lab to learn more about free applications testing.
1655 Lyell Ave, Rochester, NY 14606 USA | Tel: +1 585 889 9000