Induction Brazing in a Controlled Atmosphere
- Home
- Process Applications
- Atmosphere Controlled Brazing
Why braze in a controlled atmosphere?
Induction brazing in controlled oxygen-free atmospheres under normal or close-to-normal atmospheric pressure is known as atmospheric brazing, allowing for reduced oxidation and improved control over the process.
Benefits of Induction Brazing in a Controlled Atmosphere
-
Meets tight production tolerances with precise localized heat to small areas creating pinpoint accuracy
-
Increases production rates with faster heating cycles
-
Reduces defect rates with repeatable, reliable heat
-
Eliminates variability from operator-to-operator, shift-to-shift
-
Maintains metallurgical characteristics of the individual metals
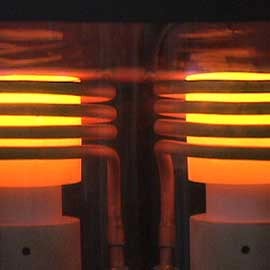
Select an option below:
controlled atmosphere brazing Application Notes
Select from our collection of controlled atmosphere brazing notes, developed over 39 years supporting our customers. Read how we helped to solve their process heating challenges!
Brazing Steel Hydraulics Fittings & Tubes
Braze steel fittings and tubes in an atmosphere to make hydraulic fittings within a targeted heating time of under 150 seconds.
Annealing steel tubes in an inert atmosphere
Induction annealing heats steel tubes to 2000 °F (1093 °C) in an inert atmosphere for very small areas within precise production tolerances. A two-turn concentrator coil is used to heat the stainless steel tube. The annealing process takes place in an inert atmosphere to prevent oxidation.
Annealing stainless steel caps (dental)
Our client had a requirement to anneal large quantities of work-hardened stainless steel crowns. Induction was suggested for its precise, controllable heating. Since oxidation is unacceptable in the finished dental product, induction heating is the appropriate choice for heating in an inert atmosphere.
A multi-turn induction annealing coil is used to heat various rod diameters. An optical pyrometer is used to measure the temperature of the part inside the induction coil. Initial static tests are conducted, then dynamic tests are run to confirm the results of the static tests
Brazing a small gas delivery assembly
This is a new part for the customer and they are developing the manufacturing process for it. The customer is interested in using induction heat for their process because they are looking for finished parts which are clean and not contaminated by any flux material. By using induction to braze the part and by doing the braze under a hydrogen atmosphere, the customer can produce brazed parts with no oxidation...
Braze a thin walled tube to a steel cap
A single turn helical coil is used to heat the quartz tube and the tube assembly. The tube assembly is held in place inside the quartz tube by a copper fixture and hydrogen is fed into the quartz tube...
Braze Copper Tube to Brass Fitting
To use induction heating to braze a copper tube to a brass fitting using a preform braze wire.
Brazing Hydraulic Hose Assemblies
To heat a steel hydraulic hose fitting in an inert atmosphere to 2200 °F within 7 seconds for brazing without any carbon buildup.
Brazing Copper Tube Assemblies
To heat a copper tube assembly in an inert atmosphere to 1450 °F within 45 seconds for brazing without flux or acid wash clean-up.
Heat twelve steel tubes simultaneously
The coil is comprised of two (2) six-position helical coils connected together in parallel to reduce the voltage requirements on the power supply.
Sintering Powdered Metals for Satellite Positioning System
A four turn helical coil is used for the sintering process. Power is applied for thirty minutes under a nitrogen flooding
Crucible Melting a variety of materials in a nitrogen atmosphere
The crucible is heated using an induction coil with a four turn pancake at the base that extends upward into a three turn helical coil.
Shrink fit a steel gear onto a steel gear motor shaft
A four-turn helical internal coil is used to heat the gear bore. The coil is inserted into the gear bore and power is applied for 90 seconds to reach the required 400 °F (204 °C) and expand the gear bore...
shrink-fitting a carbide ring into a valve seat
A three turn helical coil is used to heat the steel valve seat. The steel valve seat is placed in the coil and heated for 50 seconds to enlarge the center hole & drop the carbide ring in for the shrink-fitting process.
controlled atmosphere brazing Application Notes
Thank you Friend for trusting us with your controlled atmosphere brazing inquiries. Read any of our application notes below without registration.
Shrink fit a steel gear onto a steel gear motor shaft
A four-turn helical internal coil is used to heat the gear bore. The coil is inserted into the gear bore and power is applied for 90 seconds to reach the required 400 °F (204 °C) and expand the gear bore...
shrink-fitting a carbide ring into a valve seat
A three turn helical coil is used to heat the steel valve seat. The steel valve seat is placed in the coil and heated for 50 seconds to enlarge the center hole & drop the carbide ring in for the shrink-fitting process.
Crucible Melting a variety of materials in a nitrogen atmosphere
The crucible is heated using an induction coil with a four turn pancake at the base that extends upward into a three turn helical coil.
Annealing steel tubes in an inert atmosphere
Induction annealing heats steel tubes to 2000 °F (1093 °C) in an inert atmosphere for very small areas within precise production tolerances. A two-turn concentrator coil is used to heat the stainless steel tube. The annealing process takes place in an inert atmosphere to prevent oxidation.
Heat twelve steel tubes simultaneously
The coil is comprised of two (2) six-position helical coils connected together in parallel to reduce the voltage requirements on the power supply.
Sintering Powdered Metals for Satellite Positioning System
A four turn helical coil is used for the sintering process. Power is applied for thirty minutes under a nitrogen flooding
Brazing a small gas delivery assembly
This is a new part for the customer and they are developing the manufacturing process for it. The customer is interested in using induction heat for their process because they are looking for finished parts which are clean and not contaminated by any flux material. By using induction to braze the part and by doing the braze under a hydrogen atmosphere, the customer can produce brazed parts with no oxidation...
Braze a thin walled tube to a steel cap
A single turn helical coil is used to heat the quartz tube and the tube assembly. The tube assembly is held in place inside the quartz tube by a copper fixture and hydrogen is fed into the quartz tube...
Brazing Steel Hydraulics Fittings & Tubes
Braze steel fittings and tubes in an atmosphere to make hydraulic fittings within a targeted heating time of under 150 seconds.
Braze Copper Tube to Brass Fitting
To use induction heating to braze a copper tube to a brass fitting using a preform braze wire.
Brazing Copper Tube Assemblies
To heat a copper tube assembly in an inert atmosphere to 1450 °F within 45 seconds for brazing without flux or acid wash clean-up.
Annealing stainless steel caps (dental)
Our client had a requirement to anneal large quantities of work-hardened stainless steel crowns. Induction was suggested for its precise, controllable heating. Since oxidation is unacceptable in the finished dental product, induction heating is the appropriate choice for heating in an inert atmosphere.
A multi-turn induction annealing coil is used to heat various rod diameters. An optical pyrometer is used to measure the temperature of the part inside the induction coil. Initial static tests are conducted, then dynamic tests are run to confirm the results of the static tests
Brazing Hydraulic Hose Assemblies
To heat a steel hydraulic hose fitting in an inert atmosphere to 2200 °F within 7 seconds for brazing without any carbon buildup.
-
What parameters can limit controlled amosphere brazing with induction?
Brazing within an atmosphere is done by using a flux. This flux is not wished for in some applications the product is used for due to its corrosive nature. In addition brazing in atmosphere will result in more cleaning requirements after the joint was created
-
Why is atmosphere brazing beneficial in cold atmospheres?
Cold atmospheric brazing is typically considered low temperature joining of two metals at temperatures upto 500 degrees Celsius. This results in faster heat cycles, less power requirement, quicker cooling cycles and less distortion due to the lower temperature input.
-
What are the benefits of atmosphere brazing?
Due to the fact that brazing in an atmosphere is less complex than in an inert atmosphere the production rate is greatly increased. In addition less complex investment is required as it does not require specialized equipment to create an inert atmosphere or vacuum. Brazing in atmosphere is more versatile as setup changes are easily conducted in order to produce different parts
-
What Parameters can Limit Atmosphere Brazing with Induction?
Brazing within an atmosphere is done by using a flux. This flux is not wished for in some applications the product is used for due to its corrosive nature. In addition brazing in atmosphere will result in more cleaning requirements after the joint was created
-
Why is Atmosphere Brazing Beneficial in Cold Atmospheres?
Cold atmospheric brazing is typically considered low temperature joining of two metals at temperatures upto 500 degrees Celsius. This results in faster heat cycles, less power requirement, quicker cooling cycles and less distortion due to the lower temperature input.
-
What are the Benefits of Atmosphere Brazing?
Due to the fact that brazing in an atmosphere is less complex than in an inert atmosphere the production rate is greatly increased. In addition less complex investment is required as it does not require specialized equipment to create an inert atmosphere or vacuum. Brazing in atmosphere is more versatile as setup changes are easily conducted in order to produce different parts
-
Your induction controlled atmosphere brazing question..
Our Systems for controlled atmosphere brazing with Induction
AMBRELL CORPORATION
1655 Lyell Avenue
Rochester, NY 14606
United States
F: +1 585 889 4030
AMBRELL B.V.
Holtersweg 1
7556 BS Hengelo
The Netherlands
AMBRELL Ltd.
Unit 6, Space Business Centre
Tewkesbury Road
Cheltenham, GLOS, GL51 9FL
United Kingdom
F: +31 546 788 154