How Induction Heating Is Used
Process Application Notes
Enhance your heating processes with induction heating. Effective in a wide variety of process heating applications, improving the efficiency, repeatability and safety of your process.
- Home
- How It's Used
We've organized hundreds of application notes covering many different heating processes taken over the 39 years we've spent helping companies like yours. Select from the processes below to find the note that matches yours or suggests other induction solutions.
Headline
Add content here.
Headline
Add content here.
Headline
Add content here.
Headline
Add content here.
Headline
Add content here.
Headline
Add content here.
Headline
Add content here.
Headline
Add content here.
Headline
Add content here.
Headline
Add content here.
Headline
Add content here.
Headline
Add content here.
Headline
Add content here.
Headline
Add content here.
Headline
Add content here.
Headline
Add content here.
Headline
Add content here.
Headline
Add content here.
Headline
Add content here.
Headline
Add content here.
Headline
Add content here.
Headline
Add content here.
Headline
Add content here.
Headline
Add content here.
Headline
Add content here.
Headline
Add content here.
Headline
Add content here.
Headline
Add content here.
Headline
Add content here.
No results
About Induction Heating
Induction heating is a fast, efficient, precise and repeatable non-contact method for heating metals or other electrically-conductive materials. The material may be a metal such as brass, aluminum, copper or steel or it can be a semiconductor such as silicon carbide, carbon or graphite. To heat non-conductive materials such as plastics or glass, induction is used to heat an electrically-conductive susceptor, typically graphite, which then transfers the heat to the non-conducting material.
Read our 4-page brochure; learn more about how the science of induction technology can solve your precision heating problems.
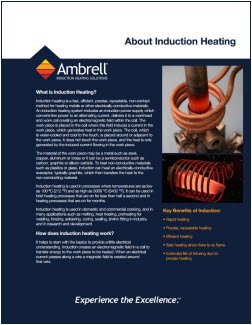
AMBRELL CORPORATION
1655 Lyell Avenue
Rochester, NY 14606
United States
Directions
T: +1 585 889 9000
F: +1 585 889 4030
Contact Sales
Contact Orders
Contact Service
AMBRELL B.V.
Holtersweg 1
7556 BS Hengelo
The Netherlands
Directions
T: +31 880 150 100
F: +31 546 788 154
Contact Sales
Contact Orders
Contact Service
AMBRELL Ltd.
148-149 Gt Charles Street
Birmingham, GL51 9FL
United Kingdom
T: +44 1242 514042
F: +31 546 788 154
Contact Sales
Contact Orders
Contact Service